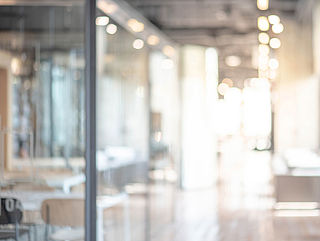
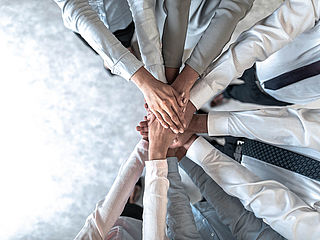
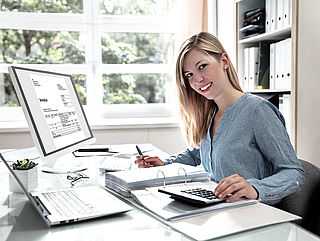
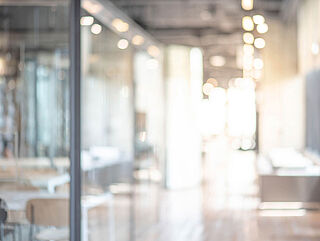
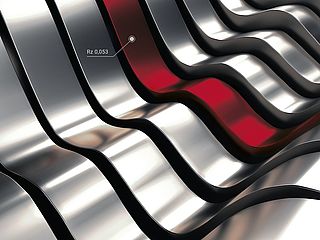
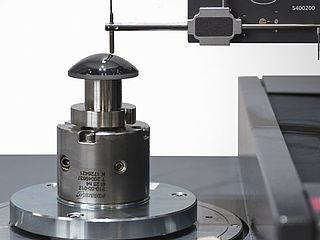
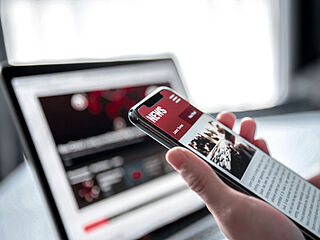
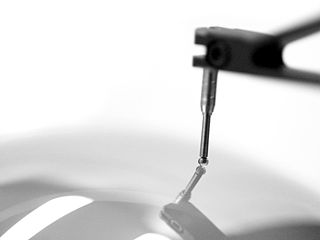
创新的计量学,应用范围广泛:
- • 长度和直径
- • 表面和轮廓
- • 形状和位置
- • 齿轮和轴
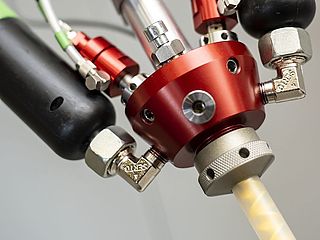
液体和糊剂的精确混合与计量:
- • 齿轮计量泵
- • 纤维生产用泵
- • 计量混合分配机以及混合头
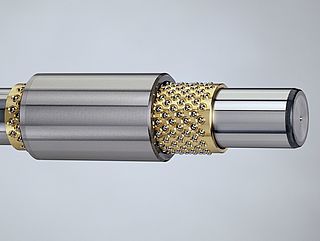
用于以下行业无间隙线性和旋转运动的转冲程轴承:
- • 机械工程
- • 精密工程
- • 光学
- • 电子
- • 以及许多其他行业
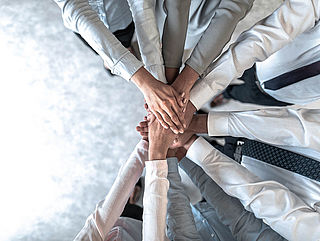
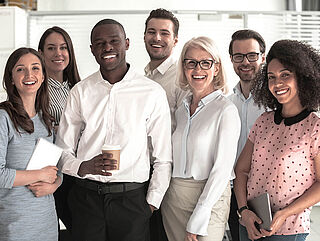
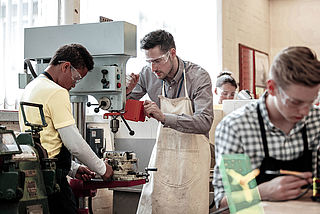
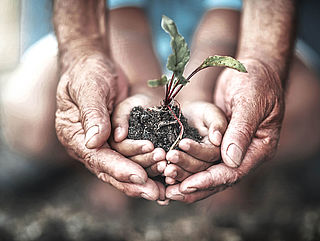
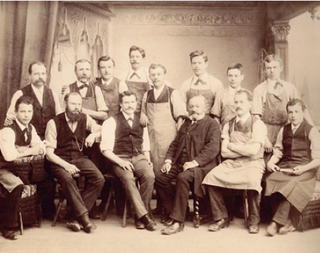
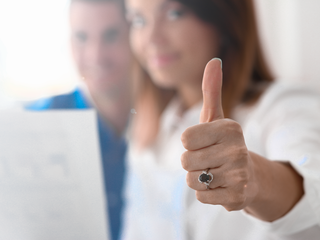
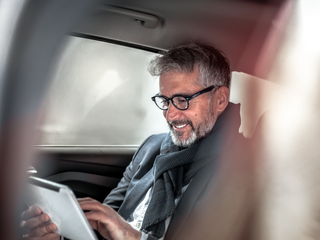
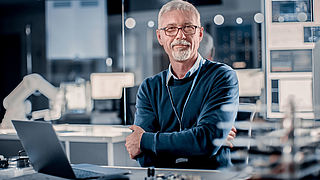
作为一家活跃于国际范围的公司,Mahr 不仅在德国拥有专利,在世界范围内也拥有专利。
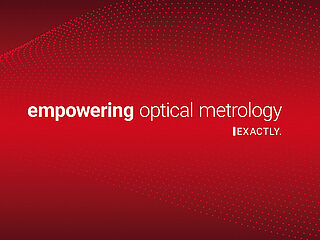
Optical or tactile surface analysis: Which measuring method is best when?
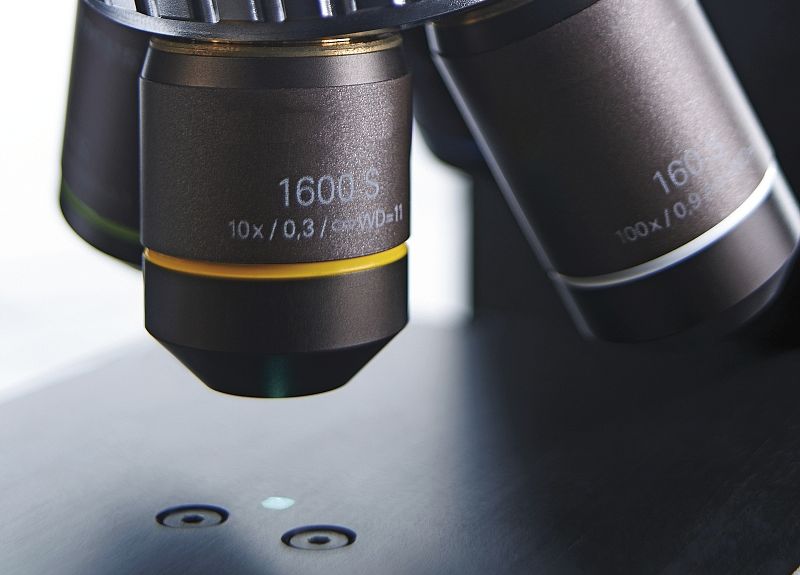
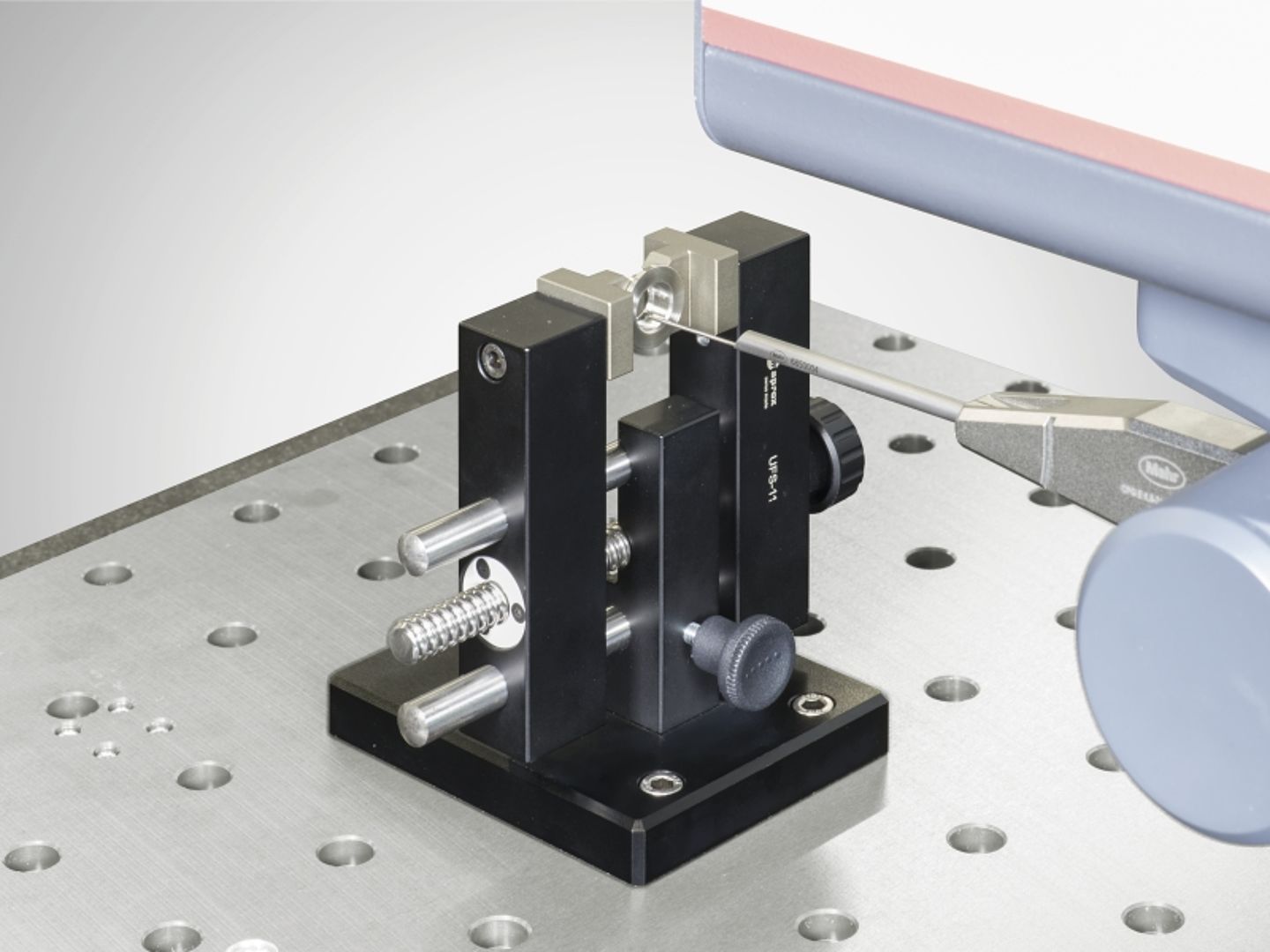
Roughness and waviness measurements have long been an integral part of quality testing. Traditionally, this is understood as a two-dimensional measurement. The result of tactile scanning is a surface section. The properties obtained can be described by a large number of parameters within DIN EN ISO 4287 / 4288 and DIN EN ISO 13565-1/2. The section relief can be compared with a two-dimensional snapshot, which, however, does not allow any statement about surface structures. However, if a production process requires precisely defined surface structures, optical measuring instruments are required.
The balancing act between smooth and rough
This statement is illustrated by the example of textured thin sheets used in the automotive industry. The smoothest possible substrate is the basis for first-class paintwork. The forming of the sheets in presses, however, requires a certain minimum roughness. This is essential for the adhesion of oil in order to reduce process disturbances to a minimum. To test the surface quality of such a sheet, both tactile and optical methods can be used. The 2D parameters Ra and Rpc used for roughness analysis, as well as the Wsa value according to SEP 1941, are comparable. Nevertheless, this information is not sufficient: In order to ensure that the surface meets the stringent requirements of the automotive industry, additional statistical data of the surface must be recorded.
Optical measuring methods for surface analysis
Sheet metal manufacturers use optical measuring instruments for this purpose - such as the MarSurf CM explorer. This confocal microscope is used to determine the frequency of existing particles as well as their size and volume in the surface. In addition, statements can be made about the size of depressions (empty volumes) and their position. Only this information can provide valuable results in terms of process technology in order to qualify the microstructuring of the surface. The corresponding 3D texture parameters as well as the operators for their determination are described in the still young DIN EN ISO 25178. It is the first international standard to consider the non-contact measurement and specification of 3D surface textures.
Conclusion
The qualified analysis of machined surfaces is based on the choice of the right measurement method. If the two-dimensional profile section is no longer sufficient for the assessment of surface structures, three-dimensional optical paths must be taken. The planar optical roughness measurement is still less widespread than the tactile variant. A look into the practice shows that both methods complement each other perfectly and are being used more and more.